
Bergami
Interex proudly represents Bergami, a global leader in innovative packaging solutions, in select U.S. states. Bergami combines cutting-edge technology with exceptional service to meet the evolving needs of customers in the cosmetic, personal care, pharmaceutical, food, and other industries. With over 1,500 machines installed worldwide and 90% of sales from exports, Bergami is renowned for its high technical standards, quality, and reliability. The company's commitment to customer satisfaction and close partnerships ensures the development of top-performing packaging systems that deliver long-term value.

Bergami End-of-Line Solutions: Streamline Your Packaging Process
Bergami offers cutting-edge end-of-line solutions designed to streamline your packaging process and boost efficiency. Our compact, flexible, and customizable machines integrate seamlessly into your production line, providing reliable and high-performance palletizing and case packing capabilities. With advanced features like robotics, intuitive interfaces, and quick changeovers, Bergami's solutions are tailored to meet your specific needs and help you optimize your packaging operations.
Bergami Videos

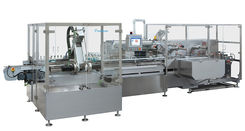
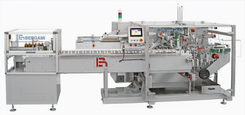
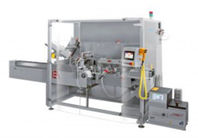




Vertical Cartoners
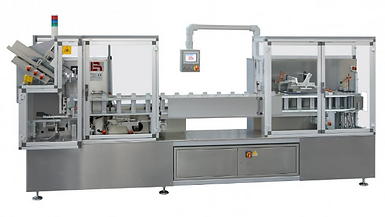
ASV 40 Cartoner
The ASV 40 cartoner efficiently packages cosmetics like creams, lotions, and perfumes. Key features:
-
"Balcony" construction for easy cleaning, maintenance, and changeovers
-
Ergonomic design for front or back loading
-
Compact, transparent design for maximum visibility
-
Adjustable timing belts for positive carton transport
-
Scratch-proof belts for package integrity
-
Touch screen control panel with self-diagnosis and help functions
-
Low noise and lubrication-free operation
Available in Standard (3 operators) and Extended (5 operators) versions, the ASV 40 is ideal for delicate products, including cartons with liners, while minimizing changeover time.
-
Size range
-
A = min. 50 mm – MAX. 220 mm
-
B = min. 30 mm – MAX. 100 mm
-
C = min. 100 mm – MAX. 240 mm
-
-
Size changeover = OPERATOR FRIENDLY
Fast and reproducible adjustments through scaled spindles with hand wheel and digital indicator plus operator guidance via operating terminal -
Mechanical speed = up to 70 Cartons per minute
-
Installed Power (Basic machine) = 2,5 KW
-
Air consumption (Basic machine) = 12 NI per minute
-
Air pressure = 5/6 bar
-
Approx Net weight = 1800 KG
-
Noise level = <72dB

Technical specifications
Horizontal Cartoners
AS 70 Cartoner

-
Size range
-
A = min. 50 mm – MAX. 220 mm
-
B = min. 30 mm – MAX. 100 mm
-
C = min. 100 mm – MAX. 240 mm
-
-
Size changeover = OPERATOR FRIENDLY
Fast and reproducible adjustments through scaled spindles with hand wheel and digital indicator plus operator guidance via operating terminal -
Mechanical speed = up to 70 Cartons per minute
-
Installed Power (Basic machine) = 2,5 KW
-
Air consumption (Basic machine) = 12 NI per minute
-
Air pressure = 5/6 bar
-
Approx Net weight = 1800 KG
-
Noise level = <72dB

Technical specifications
The AS 70 is a horizontal intermittent motion cartoner designed for medium to large-sized product cartoning applications in the pharmaceutical, cosmetic, food, and consumer products industries. Its key features include:
-
Bucket feeding chain with dedicated feeders for automatic product placement
-
Sensor for checking product presence and triggering carton and leaflet retrieval
-
Double vacuum arm system for positive carton erection, ensuring optimal performance with a wide range of cartons and cardboard qualities
-
Centrally adjustable carton transport system
-
Hand wheel and digital indicators for easy adjustment of belt transport system width to suit carton length
-
Operator-side pusher for product insertion
-
Lateral belts for carton discharge after closing operation
-
Touch screen operator interface control panel displaying machine functions, status, and fault/alarm messages
-
Adjustable speed setting for optimal production speed
-
Sturdy mechanical construction without hydraulic or oleo-pneumatic devices for enhanced reliability and durability
The AS 70 cartoner provides an efficient and reliable solution for medium to large-sized product cartoning needs across various industries.
Case Packers

-
Size range
-
A = min. 140 mm – MAX. 550 mm
-
B = min. 100 mm – MAX. 350 mm
-
C = min. 100 mm – MAX. 350 mm
-
-
Size changeover = OPERATOR FRIENDLY
-
Fast and reproducible adjustments through scaled spindles with hand wheel and digital indicator plus operator guidance via operating terminal
-
Mechanical speed = from 15 Cases per minute
-
Installed Power (Basic machine) = 3,8 KW
-
Air consumption (Basic machine) = 30 NI per minute
-
Air pressure = 5/6 bar
-
Approx Net weight = 1200 KG
-
Noise level = <72dB

Technical specifications
K 15
The K 15 is an automatic side-loading case packer designed for packaging individual or bundled cartons into pre-glued RS cases, particularly suitable when space is limited at the end of the line. Key features include:
-
Compact design, high accessibility, simple size changeover, and maximum reliability
-
Option for case sealing using adhesive tape and/or hot-melt
-
Horizontal carton magazine for easy loading
-
Positive pick-up and forced opening arms with suction cups for maintaining perfectly erected cases during product insertion
-
Precise conveyor system for positive delivery of filled cases to the sealing station
-
Mobile tunnel for product insertion, minimizing mechanical movements to improve speed, reliability, and lasting time
-
Cantilever design on both sides for great accessibility and easy cleaning
-
Fully automated operations performed by brushless motors
-
Ergonomically positioned case blank magazine on the front of the machine
-
Double arms with suction cups for case blank pick-up and transfer to the opening unit, ensuring perfect squaring
-
Vertical stacking of products inside the hopper before being pushed into the case
-
Chain conveyors for case transfer to the flap folding and taping area
-
Simultaneous adjustment of taping units depth
-
Optimal visibility during the entire packaging process
-
Automatic end-of-batch machine emptying
-
Touch screen operator interface control panel displaying machine functions, status, and fault/alarm messages
-
Adjustable speed setting from the control panel for optimal production speed
The K 15 case packer offers a reliable and efficient solution for side-loading individual or bundled cartons into pre-glued RS cases, with a focus on accessibility, ease of use, and space-saving design.
Palletizers

-
Pallet dimension
-
X* = min. 800 mm – MAX. 1000 mm
-
Y = 1200 mm
-
Z + W = 1550 mm (Standard)
-
Z + W = 2000 mm (Modification – Option)
-
-
Size changeover = OPERATOR FRIENDLY
-
Fast and reproducible adjustments through scaled spindles with hand wheel and digital indicator plus operator guidance via operating terminal
-
Mechanical speed = up to 15 Cases per minute
-
Installed Power (Basic machine) = 8 KW
-
Air consumption (Basic machine) = 30 NI per minute
-
Air pressure = 5/6 bar
-
Approx Net weight = 2000 KG
-
Noise level = <72dB
Technical specifications
P 15 Palletizer
The P 15 has been developed to meet the market requirements for flexibility and compactness in the palletizing section of modern production lines. The heart of the machine is a robot (4 or 6 axis, depending on the application) that picks up incoming cases and places them on the pallet according to a pre-set pattern stored in the machine's memory.
This ultramodern robot technology, which is in operation thousands of times throughout the world, guarantees top machine availability and low life-cycle costs over the entire productive life of the machine.
The P 15 can be equipped with a large capacity and empty pallet magazine with automatic handling of empty and full pallets. Products can be fed from single or multiple lines. Due to its modular design, the pallet handling section can be customized according to the end user's requirements.
The machine can be supplied as a standalone unit or connected to a BERGAMI side-loading case-packer, particularly where space is at a premium.
The P 15 features a standard PLC unit that interacts with the robot processor, making operation straightforward. A large and comprehensible operator interface simplifies change-overs and assists with diagnostics. The machine is fully guarded by transparent panels interlocked with safety switches and light curtains in the pallet removal area.
Key features:
-
Compatible with both US and European type pallets
-
Fanuc robots for placement
-
Automatic Palletizer arranged with single or double floor pallet station
-
Human interface for diagnostics and creation of pallet patterns
-
Quick size changeover
-
Optimal visibility during the entire packaging process
-
Automatic end-of-batch machine emptying
-
Touch screen operator interface control panel displaying machine functions, status, and fault/alarm messages
-
Adjustable speed setting from the control panel for optimal production speed
Integrated Case Packers and Palletizers
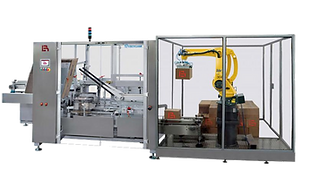
-
Case dimension
-
A = min. 140 mm – MAX. 550 mm
-
B = min. 100 mm – MAX. 350 mm
-
C = min. 100 mm – MAX. 350 mm
-
Pallet dimension
-
X* = min. 800 mm – MAX. 1000 mm
-
Y = 1200 mm
-
Z + W = 1550 mm (Standard)
-
Z + W = 2000 mm (Modification – Option)
-
-
Size changeover = OPERATOR FRIENDLY
-
Fast and reproducible adjustments through scaled spindles with hand wheel and digital indicator plus operator guidance via operating terminal
-
Mechanical speed = up to 15 Cases per minute
-
Installed Power (Basic machine) = 11 KW
-
Air consumption (Basic machine) = 220 NI per minute
-
Air pressure = 5/6 bar
-
Approx Net weight = 3200 KG
-
Noise level = <72dB

Technical specifications
KP15 Casepacker-Palletizer
The KP15 is a compact, ergonomic, and versatile automatic horizontal casepacker-palletizer that combines product packing and palletizing operations into a single, monobloc unit. Utilizing innovative robotized solutions, it offers enhanced performance in terms of speed and flexibility.
The palletizing operation is managed through the Machine HMI, a high-performance and versatile device that allows the use of two palletizing/depalletizing stations simultaneously. While one station is operating, the pallet can be changed in the other. The KP15 can be customized with various options, including printers, labelers, barcode scanners, and check weighers.
Key features:
-
Ergonomically positioned case magazine on the side of the machine
-
Fully automated operations performed by brushless motors and controlled by an Industrial PC
-
Double arm with suction cups for case pickup and transfer, ensuring perfect squaring
-
Vertical stacking of products inside the hopper before being pushed into the case
-
Servodriven lugs for case transfer to the flap folding and taping area
-
Robot for case placement on the pallet according to a pre-set pattern
-
Single or double floor pallet station
-
Human interface for diagnostics and pallet pattern creation
-
Quick size changeover
-
Optimal visibility during the entire packaging process
-
Automatic end-of-batch machine emptying
Tube Fillers

Technical specifications
-
Metal tube size range (Ø): = 10-42 mm
-
Plastic tube sizer range (Ø) = 10-50 (60) mm
-
Tube size range with cap (H) = 50-240 mm
-
Dose = 3-250 ml
-
Mechanical speed = 4 800 tubes per hour
-
Motor = 1.1 KW
-
Installed power for metal tubes = 3 KW
-
Installed power for plastic tubes = 6 KW
-
Installed power for laminated tubes = 6 KW
-
Water consumption (plastic and laminated tubes only) = 140 l/h
-
Max air consumption at 5 bar (basic machine) = 3200 l/h
-
Approx weight = 1000 Kg
TF 80 Automatic Tube Filling and Closing Machine with Cassette Infeed System
The Tube Filler Model TF 80 is an advanced automatic tube filling and closing machine designed to handle metal, plastic, polyfoil, and laminate tubes with precision and efficiency. This machine is built to meet the highest technological standards, ensuring maximum productivity and quality in tube filling operations.
Key Features:
-
Cassette infeed system for seamless tube feeding
-
Designed according to G.M.P. standards, suitable for sterile rooms and laminar flows
-
Fast size changeover without the need for tools
-
Mechanical dose adjustment or servo motor-driven (upon request)
-
Variety of filling nozzle types available, including shut-off, blow-off, cut-off, combination of blow-off and cut-off, or valve-nozzle, depending on the product being filled
-
Tube bottom-up filling with a mechanical lifting mechanism or servo motor (upon request) for precise control of tube lifting and descending based on fill product characteristics
-
Excellent access for cleaning and maintenance
-
Integrated tube sealing system
Machine Specifications:
-
Robust 304 stainless steel machine frame and control board
-
Self-lubricated components for moving mechanical parts, ensuring smooth operation
-
PLC-controlled machine operations with an alphanumeric display for user-friendly interface
-
Control panel mounted on a swiveling arm for easy access and adjustments
-
Capsized tube control device to prevent tube misalignment
-
12-position turntable for efficient tube handling
-
316 L parts in contact with the product, featuring tri-clover connections for easy cleaning and maintenance
-
Fixed injector with positive shut-off valve and nozzle cleaning air blow for precise filling and minimized product waste
-
Safety coupling to protect mechanical parts from overload, enhancing machine longevity
-
Automatic machine stop in case of insufficient compressed air supply, ensuring consistent operation
Wrappers

-
Size range
-
A = min. 60 mm – MAX. 300 mm
-
B = min. 50 mm – MAX. 150 mm
-
C = min. 25 mm – MAX. 90 mm
-
-
Size changeover = OPERATOR FRIENDLY
-
Fast and reproducible adjustments through scaled spindles with hand wheel and digital indicator plus operator guidance via operating terminal
-
Mechanical speed = from 40 to 60 Wraps per minute (according to the options installed on the machine)
-
Installed Power (Basic machine) = 2,5 KW
-
Air consumption (Basic machine) = 40 NI per minute
-
Air pressure = 5/6 bar
-
Approx Net weight = 750 KG
-
Noise level = <72dB
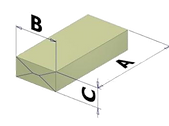
Technical specifications
CM 40: Versatile Overwrapping Machine for High-Quality Packaging
The CM40 is a renowned overwrapping machine that offers versatility, ergonomics, and maximum efficiency in a compact footprint. This machine has been successfully deployed by hundreds of satisfied customers worldwide, thanks to its flexibility and ease of operation.
Key Features:
-
Wraps products as single packs or bundles using heat-sealable materials from a reel of coated polypropylene, cellophane, PVC, and others
-
Positive gripper film feeding system enables the use of thin and challenging films
-
Film stops over the product, ensuring exceptional aesthetic quality of the overwrap
-
Excellent packaging quality
-
Highly reliable cam-driven technology
-
Competitive pricing for an entry-level machine
-
Positive unwinding of wrapping material from the roll placed in-line with the product flow direction
-
Discharge by sealing plates
-
Quick and easy size changeover with minimal tool usage
-
Flexible size range
-
Low-cost change-parts
-
Touch screen operator interface control panel displays machine functions, status, and fault/alarm messages
-
Adjustable speed setting from the control panel for optimal production speed
The CM40 is a top choice for businesses seeking a versatile and efficient overwrapping solution that delivers high-quality packaging results.
Display Box Machines

Technical specifications
-
Size range
-
A = min. 80 mm – MAX. 300 mm
-
B = min. 60 mm – MAX. 200 mm
-
C = min. 20 mm – MAX. 125 mm
-
-
Size changeover = OPERATOR FRIENDLY
-
Fast and reproducible adjustments through scaled spindles with hand wheel and digital indicator plus operator guidance via operating terminal.
-
Installed Power (Basic machine) = 4,5 KW
-
Air consumption (Basic machine) = 15 NI per minute
-
Air pressure = 5/6 bar
-
Approx Net weight (Basic machine) = 1500 KG
-
Mechanical speed = up to 60 Cartons per minute
FA 60: Versatile Top Loading Forming and Filling Display Box Machine
The FA 60 is a highly versatile machine designed for packing a wide range of products, including food, pharmaceutical, consumer goods, confectionery, and tobacco, into various carton types such as trays and displays. The machine's flexibility allows for both top loading and side loading capabilities, starting with a flat blank picked up from a magazine, which is then filled with the product(s) and closed according to the desired packaging style.
Key Features:
-
Monobloc design with balcony construction, fully compliant with GMP standards
-
Clear and easily accessible machine layout with outstanding operating simplicity
-
Ergonomically positioned feeding units
-
Continuous conveyor belt or racetrack for product infeed
-
Trouble-free alignment of blanks
-
Hopper-based blank forming, ensuring perfect carton gluing regardless of product consistency
-
Centrally adjustable toothed belt carton transport system with digital indicators ("A" and "B" dimensions)
-
Top loading or side loading of products based on the selected machine configuration
-
Ability to function as both a tray packer and wrap-around cartoner with lid closing on the same machine
-
Touch screen operator interface control panel displaying machine functions, status, and fault/alarm messages
-
Self-diagnosis function
-
Help function for quick and easy fault resolution
The FA 60's adaptability and user-friendly design make it an ideal solution for businesses requiring a reliable and efficient machine for packing a diverse range of products into various display box formats.
Tray Formers

-
Size range
-
A = min. 80 mm – MAX. 300 mm
-
B = min. 60 mm – MAX. 200 mm
-
C = min. 20 mm – MAX. 125 mm
-
-
Size changeover = OPERATOR FRIENDLY
-
Fast and reproducible adjustments through scaled spindles with hand wheel and digital indicator plus operator guidance via operating terminal.
-
Installed Power (Basic machine) = 4,5 KW
-
Air consumption (Basic machine) = 15 NI per minute
-
Air pressure = 5/6 bar
-
Approx Net weight (Basic machine) = 1500 KG
-
Mechanical speed = up to 60 Cartons per minute
Technical specifications
FA 60: Versatile Top Loading Forming and Filling Display Box Machine
The FA 60 is a highly versatile machine designed for packing a wide range of products, including food, pharmaceutical, consumer goods, confectionery, and tobacco, into various carton types such as trays and displays. The machine's flexibility allows for both top loading and side loading capabilities, starting with a flat blank picked up from a magazine, which is then filled with the product(s) and closed according to the desired packaging style.
Key Features:
-
Monobloc design with balcony construction, fully compliant with GMP standards
-
Clear and easily accessible machine layout with outstanding operating simplicity
-
Ergonomically positioned feeding units
-
Continuous conveyor belt or racetrack for product infeed
-
Trouble-free alignment of blanks
-
Hopper-based blank forming, ensuring perfect carton gluing regardless of product consistency
-
Centrally adjustable toothed belt carton transport system with digital indicators ("A" and "B" dimensions)
-
Top loading or side loading of products based on the selected machine configuration
-
Ability to function as both a tray packer and wrap-around cartoner with lid closing on the same machine
-
Touch screen operator interface control panel displaying machine functions, status, and fault/alarm messages
-
Self-diagnosis function
-
Help function for quick and easy fault resolution
The FA 60's adaptability and user-friendly design make it an ideal solution for businesses requiring a reliable and efficient machine for packing a diverse range of products into various display box formats.
Pick and Place
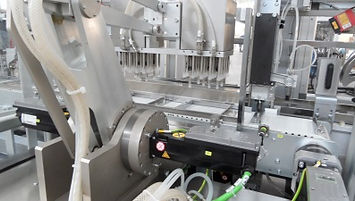
Title: 2 Axis Brutus: Versatile and Efficient Pick and Place System
The 2 Axis Brutus is a state-of-the-art pick and place system developed by Bergami, designed to streamline product collation and insertion into cartons or cartoner bucket chains. With both top loading and side loading capabilities, this system offers unparalleled flexibility in product handling.
Key Features:
-
Controlled by two servomotors for precise and efficient operation
-
Simplified format changes with full recipe retention and programming through the Machine Touch Display
-
Quick setup for new products within a fixed parameter area in the HMI, generating a new format program in just minutes
-
Versatile two-dimensional working field of 0.5m x 0.5m for normal operation
-
Tool exchanger hand design, equipped with all necessary devices for tool control
-
High-speed operation, with the Pick & Place arm capable of accelerating at 2G and reaching speeds up to 4 m/sec
-
Impressive load-bearing capacity of 20 kg, suitable for a wide range of products
-
Ability to work in teams with other Pick and Place systems, ensuring completely filled packages
The 2 Axis Brutus offers a powerful and adaptable solution for businesses seeking to optimize their product handling processes. Its user-friendly interface, quick setup, and high-speed operation make it an ideal choice for various industries requiring efficient and reliable pick and place functionality.
Mixers and Melters
Vacuum Turbo-Emulsifiers Series ES by Bergami: The Highest Technology for Processing Liquid and Creamy Products
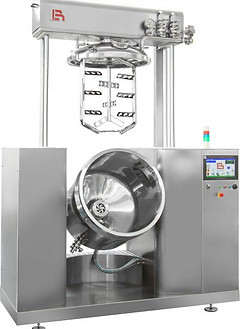

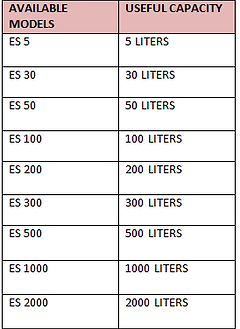
Key Features:
-
Vessel equipped to load raw materials, unload the final product, and check the process
-
Control panel with Bergami technology for essential functions (temperature, vacuum control, vessel movements) and software records of working parameters
-
Combined action of two independent and complementary movements for processing:
-
Slow mixing: coaxial movement that continuously moves the bulk and favors heat exchange using scrapers; recommended for highly viscous products
-
Fast mixing action: homogenizing group consisting of a turbine (stator and rotor) for rapid and thorough homogenization
-
-
Double-planetary slow mixer option available for medium-density creamy products
-
Universal turbine with stator and helix rotor (3-blade shaped, multi-blade shaped on ES 1000 and 2000 models) suitable for a wide range of products
-
Emulsifying group on the bottom of the vessel, made up of a turbine (stator and rotor), ensures rapid and thorough product homogenization
The Vacuum Turbo-Emulsifiers Series ES by Bergami offers a versatile solution for processing a diverse range of liquid and creamy products in the cosmetic and pharmaceutical industries, with customizable options to meet specific customer needs.
Bergami Packaging Solutions offers the Vacuum Turbo-Emulsifiers Series ES, designed to process a wide range of liquid and creamy products for the cosmetic and pharmaceutical industries. These machines are particularly suitable for emulsions (cream/milk products), serums, oils, balms, gels, and lotions, with special versions capable of processing make-up, suppositories, hair dyes, toothpastes, mud products, and shaving creams. The useful capacity ranges from 5 to 2000 liters.
Customer Support
Exceptional Quality